《当サイトは Google Adsense、Amazon アソシエイト等 アフィリエイト広告を利用して収益を得ています》
弊社では炭酸ガスボンベは1か所に置いて工場内はガス管で配管して各溶接機脇には流量計のみの設置でガスを供給しています。なので各溶接機脇に1本ずつガスボンベを置いていた時よりずいぶんと便利になりました。しかし炭酸ガスレギュレーターのヒーターは100V電源より取って年中入れっぱなしで電気代がかかっていました。
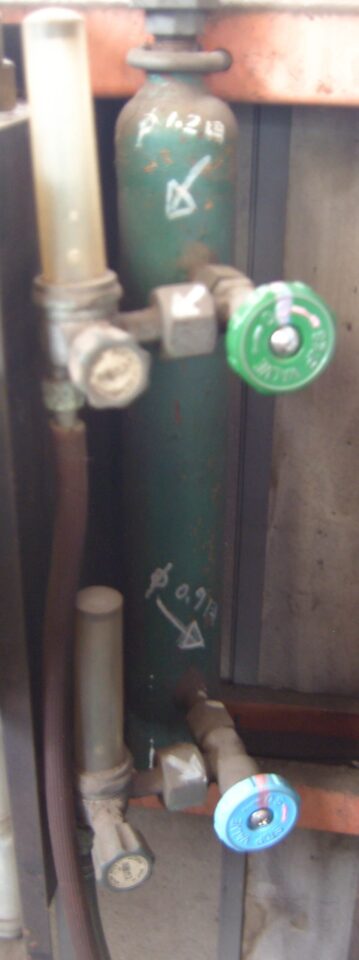
溶接機脇に設置したガス取り出し用の小型のタンクです。配管だけでも内容量が大きくあるので実は小タンクは必要ないです。既存の配管接手の組み合わせで十分でした。
ノンヒーター型の導入
ノンヒーター型の導入も考えましたが、2万円以上と高いしまだ使用してないヒーター付きのレギュレーターが2個も在庫に有るのでどうにかこれを生かした対策を考えてみました。
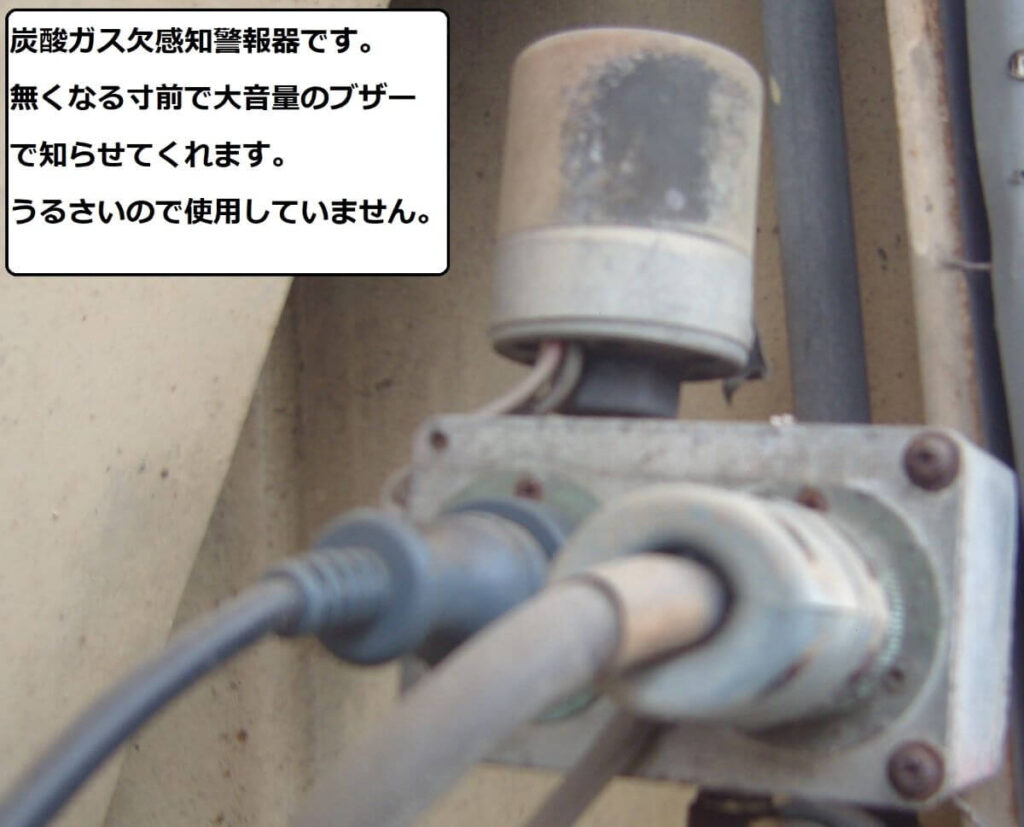
上記の物は警報機です。昔ロボット溶接機導入時に配管する基に取りつけました。いま人が手で溶接するだけですので使うのをやめました。というのもこれと一緒にヒーターの電源100vの元にタイマーを付けて営業時間内のみの通電にしていたのですが、曜日設定は出来ない安いタイマーなので日曜日などに大きな音量のブザーが鳴ることが何回かあったからです。
考えてみるとヒーターを切ると起こる不都合は出口がドライアイスで塞がれガスが出なくなることです。また液化2酸化炭素なので気化がうまく出来ず液体のまま出てきたらガス代が高くなります。なので空気の中の熱をなるべく広い表面積で受け取ればいいのではないかと思ったのです。(要はノンヒーター製品外観の真似です。。。)
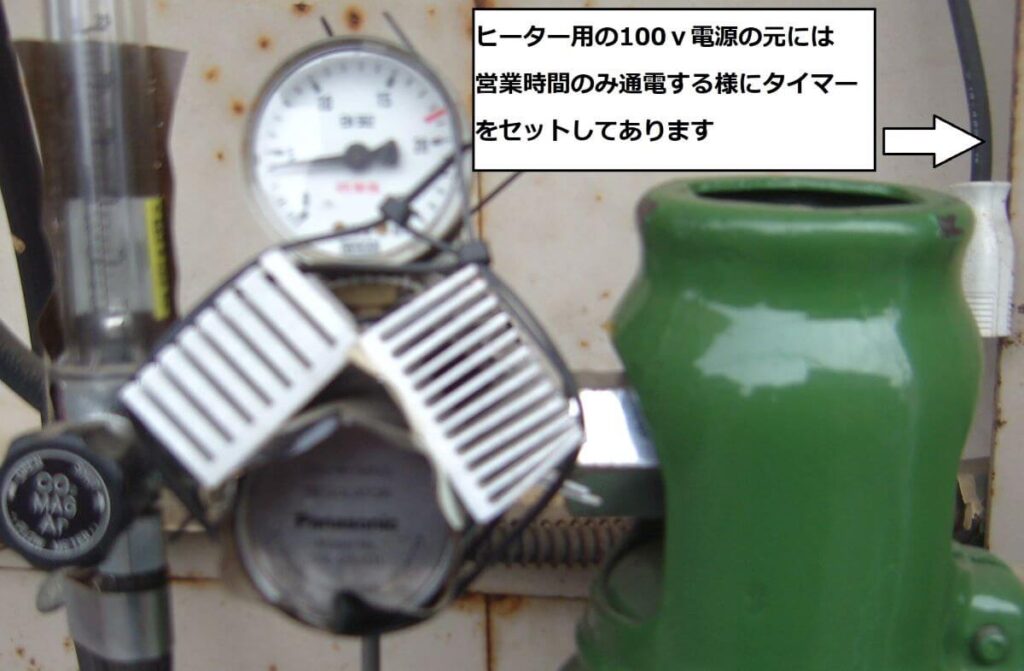
熱伝導の良いアルミ材を熱伝導テープで貼り付けました。念のため結束バンドで止めています。
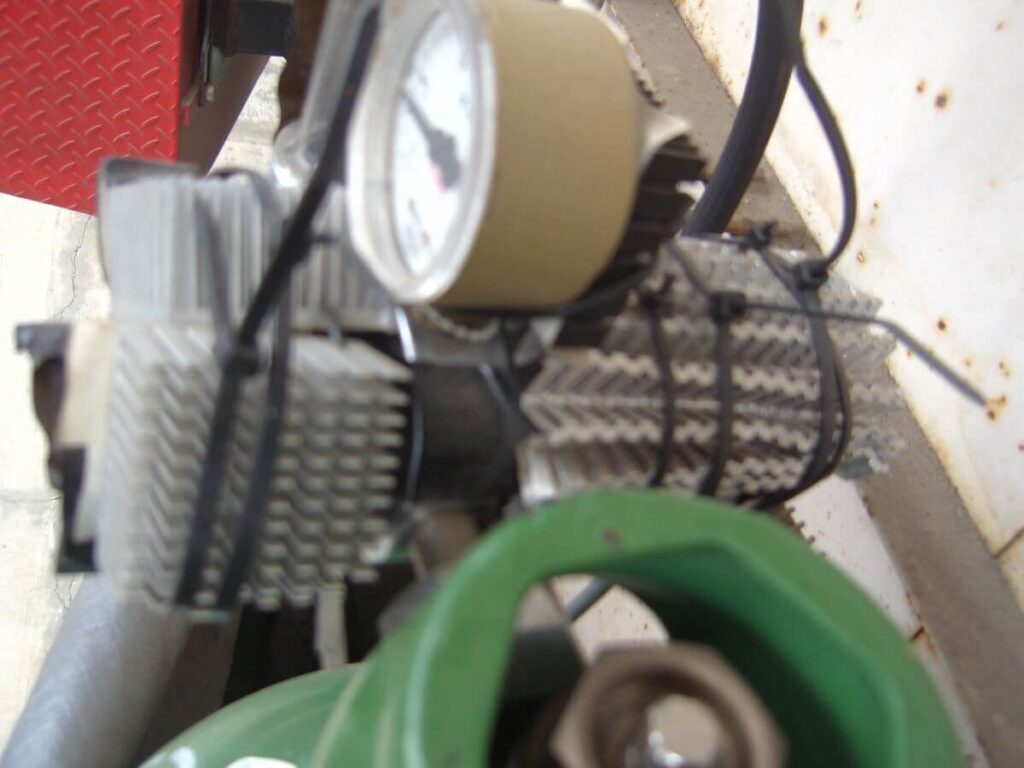
ヒーター部にもアルミ材を巻き付け落ちない様に結束バンドで止めました。見てくれは醜いですが性能は良く霜の付くことは無いです。(溶接機1台使用時のみしか確認していません。)
もう2年以上この状態で使用中です。ヒーター部分は電源をつなぐと結構熱くなっていたので結構節電になったと自負しています。しかしこれらはお勧めしているのではないです。改造はあくまで自己責任で行ってください。責任は一切負えません。
また、溶接機横にボンベを負いて使用する場合は溶接機後ろから100V電源を取る構造上その溶接機使用中のみのヒーター通電になっていると思いますのでそこまで省エネを考える必要はないとは思います。
以上です。最後までお読みいただきありがとうございました。